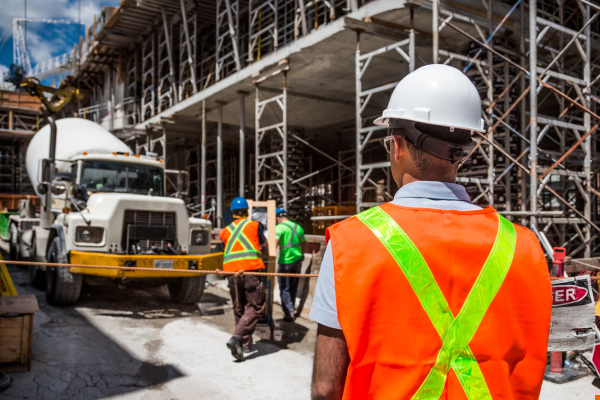
Why is there a Labor Overrun?
Daniel J. Sporer
MDCSystems®
Consultant
On a large multi-million dollar project, it shows up in the cost reports. On a smaller project, the schedule may start to show specific activity schedule slippage. The same estimator developed the bid, the project scope has not changed and your most trusted foreman says he has excellent crews. You might be experiencing labor inefficiencies and probably don’t know it. The cost reports and schedules might tell you that it occurred, but it will require additional data / analysis to determine why it has occurred and who has caused it to prove entitlement and to calculate your recovery costs.
Labor inefficiencies can occur when numerous actions are experienced on a project. However, I am going to focus on the most common types of inefficiencies that result in recoverable cost:
- Sequencing
- Overtime
- Weather
“Out-of-sequence” work does not normally show up in project reports or on As-Built schedules. Performing “out-of sequence” work occurs when the availability and turnover of access points to work areas is prohibited by other contractors working in those areas prior to the start of the next scheduled work activity. Contractors are forced to build or install equipment “out-of sequence” and are forced to constantly increase or decrease staffing levels to minimize the effects of time lost while waiting for the availability of the scheduled work areas.
An analogy of this type of inefficiency can be compared to installing railroad track. The most efficient method would be to start at one end and working continuously down the line laying track in sequence until reaching the final end point. Using this same scenario as an example of inefficiency, the track installer would place a few hundred feet of track then pick up and move his entire crew and all of their equipment 500 feet down the line and lay another few hundred feet of track in the next available work area, leaving sections of track uninstalled because the areas were not ready for the installation, thus creating “out-of sequence” working conditions. This event would happen repeatedly over the course of laying the railroad. Because of this piecemeal progression of the project, the installer would have to lay-off his workmen because work areas were not available and later rehire them when areas became available for installation. All the while the installer must ensure that all sections of the track ends would meet perfectly. With laser surveying, modern day equipment, and readily available craftsmen, this can be done, but it is not an efficient method of installation. Surely, this is not the method of installation a reasonable or competitive contractor would use to bid on a project.
Overtime is the use of labor in excess of 40 hours per person, per week. When a project is behind schedule, one of the most attempted solutions is overtime. When a schedule delay occurs, the owner usually agrees to compensate the contractor for the additional cost of the overtime differential. While this may be satisfactory for occasional overtime, this does not allow for the labor inefficiencies caused by overtime if worked excessively over an extended period of time. Working a prolonged overtime schedule can actually result in less work being accomplished than working a normal schedule. The Business Roundtable report states that by working continuous 60 hour weeks for 6 to 8 weeks you will reach a point where less work is accomplished than working a 40 hour week. This is called the “point of no return.” The U.S. Army Corps of Engineers has also published charts showing that as little as four successive weeks of overtime can reduce your productivity by up to 37%. When accepting an owners offer to pay for the differential cost of overtime, you have to consider the total hours that will be worked per week and the number of successive weeks the overtime will be performed.
Weather inefficiencies that are compensable are a result of activities in a schedule which were planned for at one time period and are being shifted into another time period. The most common example is outside work in a northern climate being shifted from summer to winter working conditions. Workers are affected by cold weather both physically and physiologically. Other weather characteristics also affect worker performance such as relative humidity, length of daylight, wind, heat, and rain. In addition to a schedule shift by the owner, if abnormal weather conditions caused the schedule shift, these can also be compensable.
The above paragraphs discussed why the labor inefficiencies occurred and who they were caused by. But, to prove entitlement, you must submit evidence that the inefficiencies caused damage to you. You will now need to analyze the schedule and cost reports to determine the extent of your damages. A widely accepted method of measuring labor productivity losses is known as the “measured mile method”. “Measured Mile Process” by Thomas W. Presnell, C.C.C., published November 2003 in the Cost Engineering manual, describes in more detail previous cases where this method has been used. Mr. Presnell states in his article, “There are many methods used by contracting parties to deal with production inefficiencies issues, however the measured mile method is the most credible and widely accepted method.” The measured mile method usually compares the productivity on identical work items during impacted and un-impacted periods of the project to determine the loss of productivity resulting from the impact. However, sometimes it is not possible to use an un-impacted period of time for this comparison. When this occurs, base bids or un-impacted time periods can be used in combination with historical data to calculate the inefficiency damage that occurred.
When all the above is performed, it is then assembled into an inefficiency claim document and submitted to the Owner/Contractor. The claim document should at least contain:
- A brief description of the problem
- An explanation of why the inefficiencies are the fault of the Owner/Contractor
- A base schedule compared to the most current schedule
- Calculations of the inefficiencies that occurred
- Calculation of the monetary damages needed for recovery
A successful inefficiency claim will convince the Owner/Contractor that you are not responsible for the poor productivity and the requested damages are indeed fair.
0 Comments