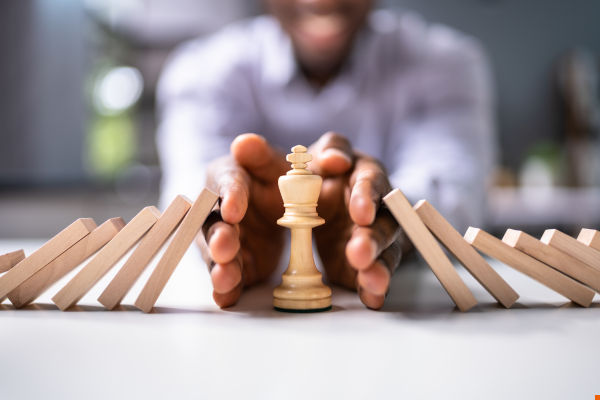
Risk Management: Insuring Continuity of Supply
James W. Haile Jr.
C.P.M., of JWH & Associates
Over the last several years, supply management professionals have been spending a majority of their time in creating, implementing and managing Business Continuity Planning (BCP) for critical products, materials and services. BCP is a strategic management process that focuses on insuring continuity of supply. The main objective is to identify and minimize or eliminate business interruptions in the event of a catastrophic event or major incidents occurring within the supply chain that can lead to adverse consequences for your business. Ten to twenty years ago, supply disruptions were caused by major snow storms, truck breakdowns, labor strikes, fire or explosions, electrical outages, machine breakdowns or even a truck driver making an unscheduled social visit.
In today’s global business environment, business supply disruptions have greatly expanded in scope. They now include and are not limited to the following:
- Pandemic Diseases
- Terrorist Acts (i.e. 911 or bio-threats)
- Acts of God (i.e. Hurricane Katrina)
- Economic Downturns (company bankruptcy)
- Rebels/Pirates
- Off Shore Non-Spec Materials
- Global Political Shifts
- Info Systems Crashes (i.e. internet/blackberry)
- Energy Outages (fuel/gas/electricity)
- Bio-contamination
- Critical Management Absences (i.e. dismissals, illness or death)
In order to mitigate your supply chain risks, BCP must be developed and integrated into the annual planning process and into the everyday business behavior. The process must be proactively supported by top management and the necessary resources (people, time, money and training) must be available in order to execute all activities. Activities would include the following:
- Training key work force for risk management skills
- Identification of critical products, materials and services to be protected
- Understand negative impact on customer base/financial bottom line re supply losses
- Prioritize above
- Collaborate with suppliers/understand their BCP options and determine adequacy
- If supplier’s plans not adequate, develop mitigation options, prioritize, conduct trials, implement final solution and document
- Track and monitor supply chain/supplier’s financials/world events/weather
- Maintain vigilance for new threats and business risks over time
In terms of mitigation of risk solutions, you really must understand your supply chain, your suppliers, the products, materials and services you acquire, how they are used within your supply chain and the risks. In addition, developing solutions, prioritizing and implementing are not activities that are solely managed by the supply management professional. These activities should occur in team collaboration with your business partners including engineering, manufacturing, quality, finance and marketing.
In terms of mitigation solutions, here is a list that should be considered:
- Have multiple suppliers that are qualified which you may or may not utilize
- Your critical supplier has an alliance with another qualified supplier
- Your supplier has multiple sites that are qualified
- Maintain a larger inventory on your site
- Have supplier hold inventory in another location
- Utilize your own transportation carriers
- Utilize supplier’s R&D site if possible for short term production
- Identify and train a temp work force
- Train your supplier re Risk Management
- Change non-critical specs (i.e. printing process: gravure versus flexographic)
- Use alternate materials for a short time
- Identify and train back-up personnel
- Use alternate types of energy
- Track weather, economic, supplier’s finances and political conditions
- Have suppliers provide their Business Continuity Plan and Communications Process
It should be obvious that keeping the lines of communications open, both in and out of your company, is a very important tool that should be actively used as part of your BCP process. As an example for dealing with your supplier base, here are some samples of verbiage that could be put in contracts or just used in email correspondence:
A. Key Contract Clauses
CRITICAL COMMUNICATIONS
It is expected that both Parties will make reasonable efforts to communicate thoroughly and within a timely manner any critical activities, business occurrences, potential issues or emerging problems that could jeopardize the quality and continuity of Services.
Examples that may fall within this category, but should not be limited to these examples are: pending labor union negotiations, planned holidays, work stoppages, maintenance shutdowns, local and national regulatory/political issues, economic issues, diseases, weather, transportation issues, critical management absences and major plant accidents. The Parties’ communicating behavior must be proactive and open in order to minimize/eliminate any negative consequences affecting the operating sites, its customers or any aspects of the supply chain affecting third parties involved in the manufacturing of critical products, materials or services. The lines of communication should be maintained as previously stated within this document.
B. Email Correspondence or Contract Clause
For the purposes of this document, as related to your particular business, please provide in some detail your Business Continuity Plans and Communications Process that you provide to your customers.
In addition, because of the severity of Global Pandemic Diseases such as H1N1 which can affect the workforce and the potential contamination of products, materials or services when handled by the workforce, our company requires the following minimum behavior and actions from our suppliers:
- Your Management Team in place to monitor H1N1 severity within the local region, track absenteeism with the work site and make decisions concerning work site operations in response to H1N1 changing conditions. This includes Coordination and communication in place with local Public Health Departments to understand regional absence recommendations.
- Educational information and resources to keep personnel aware of self-monitoring and preventative actions necessary to reduce the opportunity for becoming ill or spreading the H1N1 infection. (e.g. Literature, sanitizers etc.)
- Plans developed and tested that will enable delivery dates and quantities to be met if a potential reduced workforce becomes necessary or the site needs to close operations due to H1N1. Defined processes for mitigating workplace infections. This includes identifying available human resources as well as the procurement of supplies to perform door screening, increased facility cleaning and applying a standardized approach for addressing ill/infected employees.
- Communication plans in place to keep employees and customers updated.
Please confirm that you can comply (comparable plan available) or will comply with the four bullet points documented above.
As this article comes to a conclusion, you should have a good overview of BCP, why it is important, its’ components, who should be involved, some mitigation solutions and some verbiage to use with your supply base. Proactively managing your business risks is the only method available to insure continuity of supply for your products, materials and services. In today’s turbulent and unpredictable global business environment, BCP is a strategic management process that must be learned and utilized on an on-going basis in order to support the survival of your business assets, customer base and revenue.
This article was authored by James W. Haile Jr., C.P.M., of JWH & Associates, a supply management solutions company that specializes in supplier management & performance, negotiation training and supplier diversity development. For further contact, call 610-490-0470 or email: jwhaile@netzero.net
0 Comments